4 Easy Facts About Alcast Company Shown

There are numerous small differences between functioned and cast light weight aluminum alloys, such as that cast alloys can have extra considerable amounts of various other steels than wrought alloys. But the most notable distinction in between these alloys is the construction process where they will go to deliver the end product. Besides some surface area therapies, cast alloys will leave their mold and mildew in nearly the precise strong type wanted, whereas wrought alloys will go through numerous alterations while in their solid state.
If you believe that a wrought alloy may be the very best for your job, have a look at a few of our posts that explain more regarding details functioned alloys, such as Alloy 6061 and Alloy 6063. On the various other hand, if you assume an actors alloy would certainly be much better for you, you can find out a lot more regarding some cast alloys in our Alloy 380 and Alloy 383 write-ups (coming quickly).
Excitement About Alcast Company
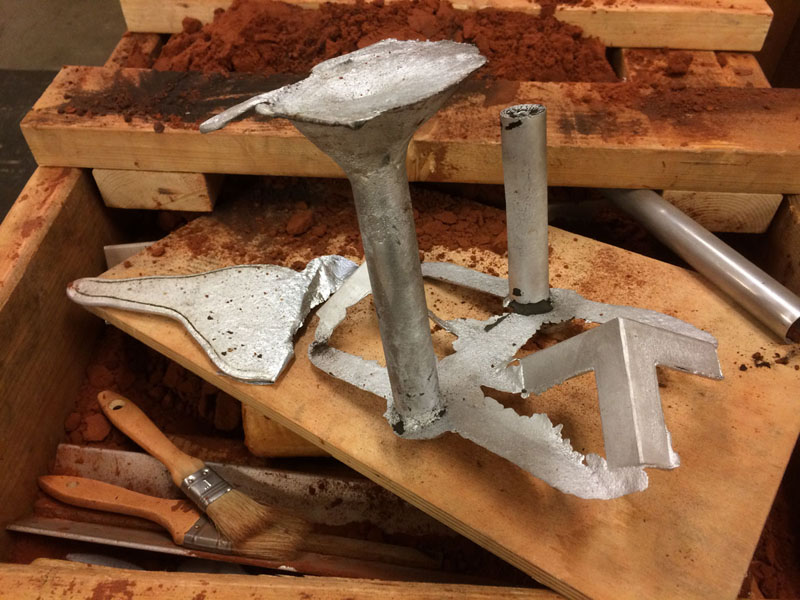
Having the experience and market expertise to engineer your castings for optimal manufacturing and quality outcomes will certainly improve the project. Producing aluminum castings needs a complicated collection of procedures to attain the appropriate results. When picking a brand-new aluminum foundry to partner with, guarantee they have extensive industry experience and are well-informed regarding all elements of the light weight aluminum casting process: layout, manufacturing, material analysis, and item screening.
The 15-Second Trick For Alcast Company
No matter the sub-process, the die casting process can be broken down right into six actions. After the purity of the alloy is examined, dies are developed. To prepare the needs spreading, it is very important that the dies are tidy, so that no deposit from previous productions stay. After cleansing, the ejection lubrication is put on the die to ensure a smooth release.
The pure metal, likewise referred to as ingot, is added to the heating system and maintained at the molten temperature of the steel, which is after that moved to the shot chamber and infused into the die (Foundry). The pressure is then preserved as the steel strengthens. As soon as the steel strengthens, the cooling procedure starts
Examine This Report about Alcast Company
The thicker the wall of the part, the longer the cooling time as a result of the quantity of interior steel that additionally requires to cool down. After the element is totally cooled down, the die halves open and an ejection device presses the part out. Adhering to the ejection, the die is shut for the following injection cycle.
The flash is the extra product that is cast throughout the process. Deburring removes the smaller items, called burrs, after the cutting procedure.
Alcast Company Can Be Fun For Anyone
Nonetheless, this proved to be an inaccurate examination, since the tester might cut right into an item and miss a location with porosity. Today, top suppliers use x-ray testing to see the whole inside of parts without cutting into them. This permits them to extra accurately accept or deny components. To get to the completed item, there are 3 primary alloys used as die casting product to pick from: zinc, light weight aluminum and magnesium.
Zinc is one of the most used alloys for die spreading due to its reduced cost of raw materials (Aluminum Casting). Its rust resistance additionally permits the components to be lengthy enduring, and it is one of the more castable alloys due to its reduced melting point.
What Does Alcast Company Mean?
As mentioned, this alloy is just one of one of the most frequently used, yet manufactures will, at times, choose aluminum over zinc due to light weight aluminum's manufacturing advantages. Light weight aluminum is extremely economical and among the much more functional alloys. Aluminum is made use of for a variety of different items and industries anything from home window frameworks to aerospace products.
Comments on “Unknown Facts About Alcast Company”